TPSynergy.com

Inventory Visibility
Inventory visibility goes beyond the limitations of the ERP system. It encompasses inventory spread across various locations such as Vendor Managed Inventory (VMI), 3PL Warehouses, and even inventory in transit. For supply chain managers, inventory visibility presents one of the most critical challenges they encounter.
​
While the ERP system provides visibility for inventory within the company, optimal conditions demand visibility throughout the extended supply chain. This includes the following key areas:
​
Vendor Managed Inventory:
With vendor-managed inventory, the responsibility for monitoring inventory position and maintaining a specified level rests with the vendor. This inventory can be located at vendor-owned premises, the customer's main warehouse, or even within a 3PL storage facility. To ensure seamless operations, complete visibility of the inventory becomes essential. For inventory maintained within the customer premises and at a 3PL location, continuous access to inventory information is crucial.
TPSynergy addresses this need by offering a unified inventory platform accessible to all involved parties. The inventory data is synchronized to the TPSynergy platform through electronic integration.
By enhancing visibility across the supply chain, TPSynergy empowers supply chain managers to overcome the challenges associated with inventory management.
​
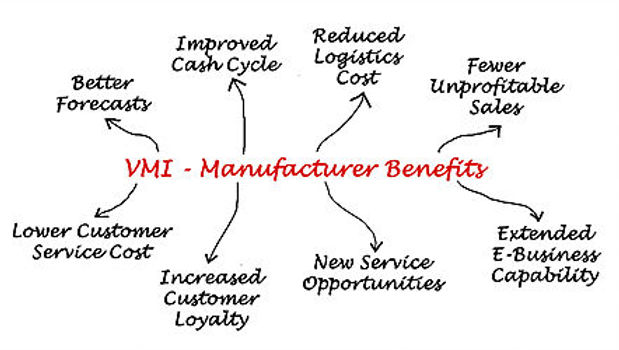
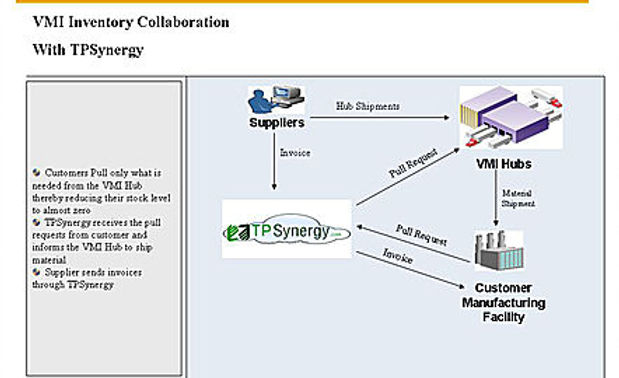
Inventory Management with Contract Manufacturers and Co-Packers:
In various industries, contract manufacturers, or co-packers in the food processing sector, play a crucial role. While customers own the product, the manufacturing and packaging processes are entrusted to these partners. It is essential to ensure that contract manufacturers maintain sufficient inventory to fulfill production requests. Typically, customers issue purchase orders directly to suppliers, which are then delivered to the contract manufacturer's facility. However, customers need up-to-date inventory information from the contract manufacturer's location for their MRP systems to issue purchase orders in a timely manner. TPSynergy offers comprehensive contract manufacturing solutions that synchronize inventory data from the contract manufacturer's facility with our cloud platform, allowing customers to access inventory positions seamlessly. Even small contract manufacturers and co-packers can easily maintain inventory data in Excel format and upload it to TPSynergy.
Consigned Inventory with Customers and Distributors:
Consigned inventory differs from vendor-managed inventory and refers to the inventory held by customers and distribution channels. TPSynergy provides visibility into this inventory by collecting real-time inventory updates either through electronic integration or periodic Excel uploads. While large customers prefer EDI integration for inventory updates, small and medium-sized businesses often opt for Excel-based solutions.
Retail Inventory Management:
Retail inventory encompasses the inventory present on store shelves. Depending on the contract, this inventory may belong to the supplier or the customer. TPSynergy utilizes EDI inventory feeds to obtain accurate information on retail inventory across multiple stores. This valuable data aids in effective demand planning and replenishment forecasts.
Third-Party Logistics (3PL) Inventory Management:
When partnering with third-party logistics providers (3PL), the management of inventory falls under their responsibility. Suppliers directly ship to 3PL warehouses, and customer orders are fulfilled from these facilities. As access to the 3PL provider's ERP system is restricted, customers are unable to view real-time inventory status. TPSynergy bridges this gap by collecting inventory updates from 3PL providers and making them available to customers in real time. This ensures seamless inventory management for all parties involved. Synchronizing inventory data with the customer's back-end ERP system ensures seamless coordination among all systems. This Supply Chain Integration as a Service maximizes efficiency.
Inventory In-transit:
Monitoring shipments in transit is a critical visibility requirement in the supply chain. These shipments, although vital, often get overlooked as they are neither with the suppliers nor with the customers. Sometimes, they even get stuck in customs due to missing documents.
TPSynergy proactively monitors in-transit inventory and promptly alerts if it is not received within the expected timeframe. Leveraging Internet of Things (IoT) devices, TPSynergy ensures close monitoring and timely corrective actions for delayed shipments.
Providing visibility into these situations can be quite challenging. However, TPSynergy offers a collaborative platform that synchronizes inventory for enhanced visibility. Whether it's through advanced Electronic Integrations, file uploads, or manual updates, TPSynergy empowers users with the inventory visibility they need.
Moreover, proactive monitoring capabilities notify users when inventory levels fall below or exceed optimal thresholds. A comprehensive dashboard provides a global view of inventory, highlighting potential problem areas.
Take control of your inventory with TPSynergy's engaging and efficient solution.

How does it benefit your supply chain?
-
Removes latency and time lag between customers and suppliers in communicating supply chain transactions
-
Purchase orders, order acknowledgments, ASNs, receipts, and inventory statuses are all synchronized between systems automatically
-
Manual data entry, associated errors, and delay is removed
-
Supplier performance and metrics improve drastically
-
Manual data entry, associated errors, and delay is removed
-
Changes in demand are propagated quickly to the entire supply chain resulting in increased customer response and satisfaction
-
It all matters for On-Time Delivery.